Prevent and Monitor Shipping Damage in Real-Time to Improve Profits
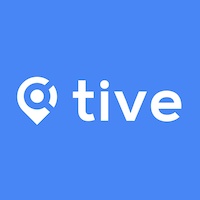
August 2, 2020
July 8, 2025
x min read
.png)
Before freight monitors and trackers came around, there is no telling what condition a product will be in when it reaches its destination. More often than not, the goods arrive in good condition. However, there are those scenarios when something happens to them while in-transit, and this is what every company seeks to avoid.
Shipping always comes with a risk, and there are numerous ways damage can occur to products in transit. The goods can arrive broken, can suffer water damage and so many other things. They can not even arrive at the destination at all in the event that they were stolen.
In any case, customers will expect the shipper to replace the damaged goods.
The types of damage include:
- Physical damage (crushed, tears, rips, etc.)
- Water damage
- Spoiled food due to incorrect temperatures
- Theft
- Infestations
Shipping damage is a costly endeavor for the merchant and will most likely put a damper on profits, especially if the shipment was large. Luckily, there are ways to significantly reduce the risk of damages.
Why does shipping damage happen?
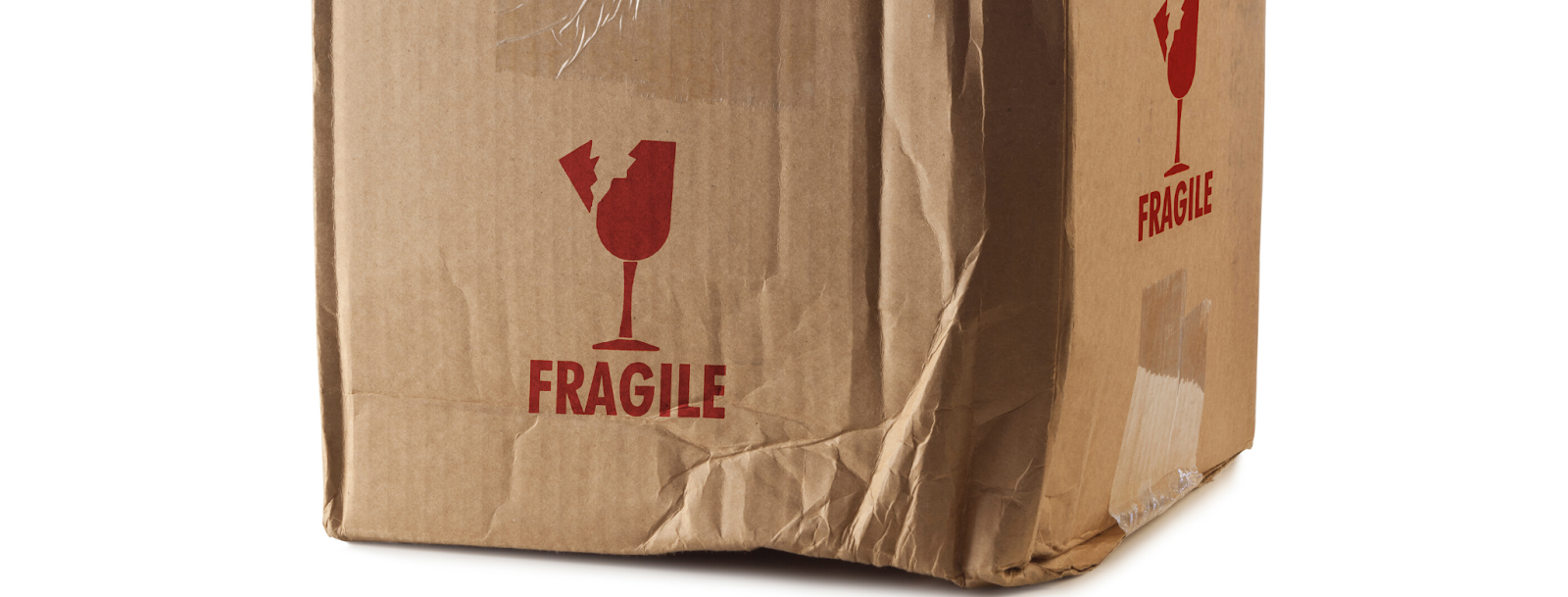
Before we talk about how to prevent damage from happening, let us talk about what leads to shipping damage in the first place. No customer will accept damaged items, and better understanding how damage can occur when a shipment is in transit is the first step to preventing it. While there are many things that can happen, here are the most common causes of shipping damage:
Empty space in the package
When the shipping company ships the goods, they can travel by various means to their destination. Through air, sea, over the road, etc. For example, if they are traveling by plane, the plane can come across some major turbulence, which can subject the goods to excessive vibrations.
Suppose the goods were placed in boxes that are bigger than the goods themselves. The turbulence will cause the goods to be tossed around due to the lack of padding. This can lead to damage, especially if the goods contain sensitive components and/or are fragile.
Not enough dunnage
Dunnage is simply any material that is used to protect goods from any form of damage, whether it is from physical impact or moisture. Examples of dunnage include bubble wrap, foam, air pillows, wood, steel, corrugated paper, solid plastics, and more.
With there being several different types of dunnage, the type you use will depend on the product being shipped.
If you find that your boxes keep arriving damaged, despite being properly packed, then the problem might be that you aren’t using enough dunnage. Depending on the product, different dunnage is required to absorb impacts or moisture in order to arrive at their destination safely.
Improper handling
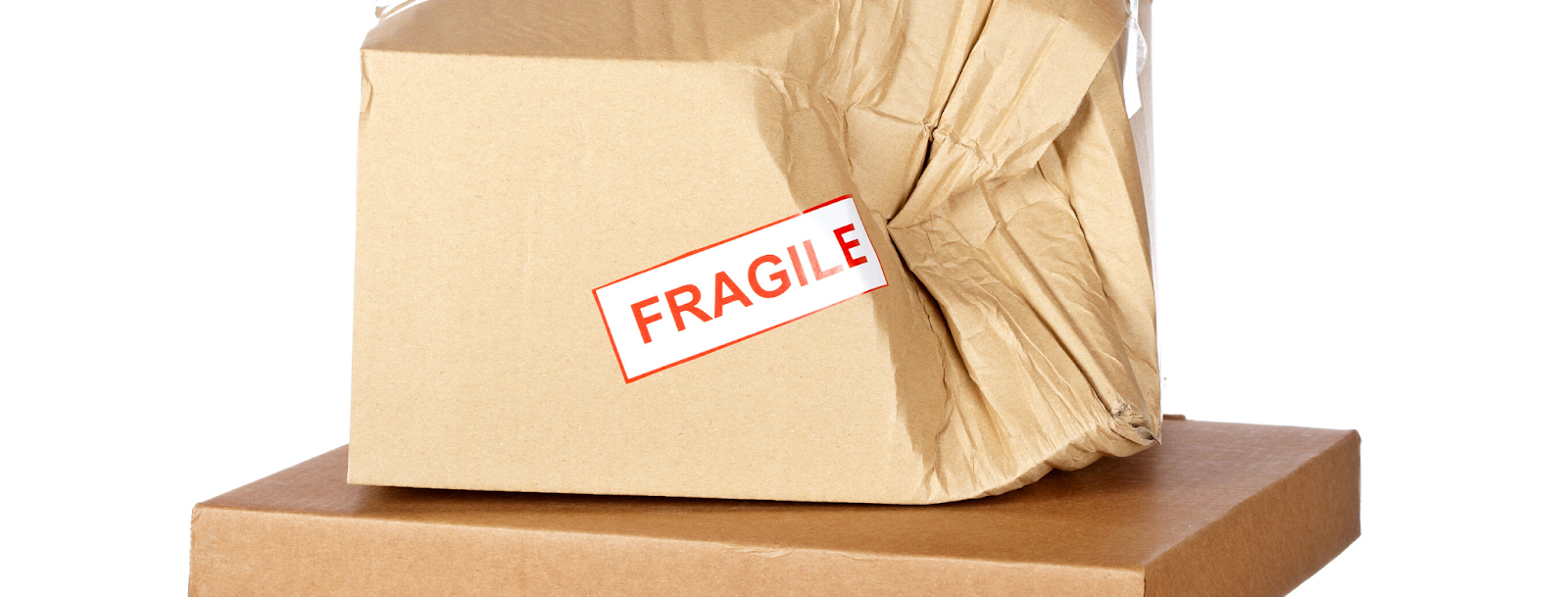
In an ideal scenario, shipments would go from the warehouse and directly into the hands of the customer. However, that is not always the case. In between, the shipment will exchange a lot of hands, and you can’t always expect the people doing the handling to handle them in a manner that will not lead to damage.
Improper handling is what leads to many damage claims. There are precautions one can take to ensure that improper handling doesn’t occur (we will mention one in a bit), but even those are not always followed by the people doing the handling. This is why it is best to use multiple preventative measures to protect goods.
Theft
When a shipment is damaged, at least the goods are recoverable. They can be repaired and shipped back to the customer or resold at a lower price to recoup some of the costs. However, sometimes the goods can be stolen, leaving the shipping company and/or merchant with the task of fully replacing the goods.
Granted, theft is not a type of damage, but it is costly nonetheless. Theft can occur anywhere along the supply chain and should be prevented at all costs since it affects everyone. Luckily, if the shipping company has put the right anti-theft measures in place, the goods can be recovered and delivered to the customer.
Water and humidity damage
Many shipping companies have open containers only to find that the goods have suffered some form of water and humidity damage. This can be confusing, considering that the company did everything to ensure that the shipping container didn’t come in contact with any water. However, cargo has been known to “sweat”, causing "container rain".
Basically, temperature and relative humidity inside the container fluctuate due to environmental and weather changes. These external changes are no one’s fault, but they can lead to excessive condensation. Since containers aren’t airtight or watertight, the condensation can build up, leading to “cargo sweat” / "container rain" and the goods suffering from water and humidity damage.
However, the source of the condensation is not always external.
Sometimes the cargo itself and the type of dunnage used, combined with other external factors, can lead to water and humidity damage.
How to prevent shipping damage
Now that you know some of the ways in which shipping damage can occur, here’s how you can prevent it:
Fill empty space
If the item is small, make sure the box you are shipping it in isn’t large. When you place the items in the box, there should be a little space left – it shouldn’t be a tight fit. With the little extra space, put some dunnage there to protect the items, as well as some dunnage on the outside to protect the box.
Use the right dunnage
As mentioned earlier, you need to use the right dunnage for the job to prevent freight damage. If shipping fragile material (think of glass), then bubble wrap can do the trick. If moisture damage is usually the problem, then you need to use corrugated paper.
Properly label fragile packages
One of the ways to prevent improper handling is to use a “Fragile” label. The hope is that when the person handling the goods sees it, they will know that the items need to be handled delicately. Make sure to put it on all sides of the box and in a large font to make sure that the handler doesn’t miss the label.
Buy shipping Insurance
Just because you have labeled a box as fragile, it doesn’t mean that people will treat it as such. And sometimes, damage cannot be avoided altogether due to the fault of no one. While buying shipping insurance will not prevent the damage from happening it will play a huge role in cushioning the financial blowback, making it worth it.
Use GPS monitors, trackers to detect impact, shock, and temperature excursions
Some GPS trackers are outfitted with sensors that can alert you of temperature and humidity changes that can damage the goods. They can also detect and alert you of any excessive shock or impact, allowing you to secure the integrity of the goods. And should the goods get stolen or go missing, they can provide the location, allowing you to recover them.
Collect and review data on shipping damages
When you are experiencing recurrent damage with shipments, collecting data on it can contribute towards preventing it. Finding out what got damaged, as well as how and where is extremely important. When you review the data, you can identify the root cause of the problem and resolve it, preventing the damage from happening.
Prevent, Monitor and Track Shipping Damage with Tive
Tive offers GPS solutions that allow to you prevent and track shipment damage. Tive’s tracker portfolio provides global connectivity and long-lasting battery life, allowing you to track and monitor your shipments in real-time anywhere across the world for extended periods. And with the built-in shock and temperature sensors, coupled with real-time alerts, you can prevent costly damage to your goods before it is too late.
Get started with Tive today! Request our prices by clicking the button below to learn how Tive can help.
{{cta('88b4d430-cdbd-449d-bf4c-c1c395be8509','justifycenter')}}