How to Improve Exception Management with End-to-End Supply Chain Visibility
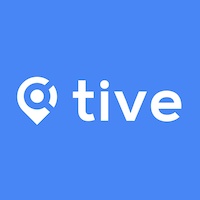
October 27, 2021
July 8, 2025
x min read
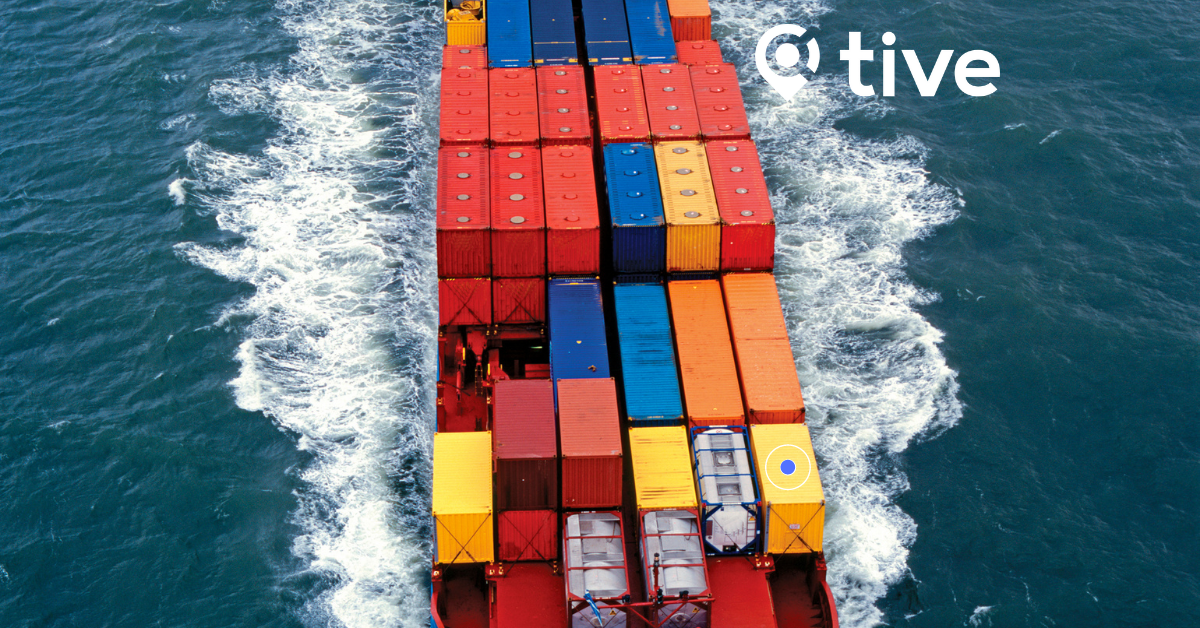
It’s not a matter of if disruptions will occur in the supply chain, it’s only a matter of time until the unexpected strikes and creates an exception. An exception does not necessarily guarantee a late delivery; it simply means a roadblock or challenge has arisen that requires immediate attention. This is why end-to-end visibility in a supply chain is so important. The more real-time information you have regarding the location and condition of shipments the more proactive you can be with exception management. Immediately informing customers of any issues and the steps being taken to mitigate them will go a long way toward nurturing customers into brand ambassadors that will help grow your business.
Let’s take a closer look at shipping exceptions and the need for strong exception management in supply chains and how a lack of end-to-end visibility can hinder those efforts. As an added bonus, we offer five sure-fire ways an end-to-end visibility solution can help improve exception management in any supply chain.
Shipping Exceptions & Exception Management in Supply Chains
There are plenty of reasons why delivery exceptions occur with in-transit packages. Here are a few of the most common:
- Inaccurate shipping labels – Among the most common of all delivery exceptions occurs when the address on a package’s label is incorrect, unclear, incomplete, or undeliverable. It can take several hours or even days to track down the correct information manually.
- Missed drop-off – Even when the delivery driver shows up on time and to the correct location, an exception occurs because no one is there to sign for a package that requires a signature to complete the final-mile delivery process.
- The package goes MIA – Arguably the most severe exception, a package that goes missing for whatever reason could take days, weeks or even longer to locate.
- Inclement weather or another force majeure – Winter storms, tornadoes, flash floods, hurricanes, earthquakes, and wildfires are just a few examples of the things Mother Nature can dish out that lead to delivery delays.
- Damaged packages – Sometimes it’s the shipping label that either gets knocked off or becomes illegible while in transit. Other times it is damage to the packaging itself that renders a shipment undeliverable. With the latter, a replacement should be sent out immediately.
- Federal holidays – Major carriers most likely will operate with bare minimum staffs, if they operate at all, on days that are designated as federal holidays and observances.
- Customs and clearance delays – International shipments often get stuck at the border due to missing documentation, labeling issues, or a staffing shortage.
- Yard exceptions – Deliveries are often marked as completed because the shipment is within a certain distance of the destination when, in fact, the truck is sitting at a truck stop.
Lack of End-to-End Visibility = Exception Management Struggles
Normally exception management is tough enough. Without end-to-end visibility, it’s almost impossible to gain meaningful insights that need to be communicated to customers. The lack of real-time location and condition data in visibility solutions slows down response times and puts stakeholders in a reactive rather than proactive mindset. Having to send emails, make phone calls, and interpret legacy data associated with past shipments compounds the level of complexity. An end-to-end visibility solution that does not include configurable real-time status alerts (location, temperature, humidity, shock events, light exposure and more) is of little or no use when trying to prevent:
- Destroyed shipments, such as pharmaceuticals and vaccines
- Rotten perishables, such as fruits and vegetables, dairy products, and meats
- Loss of upset customers
- Fines and legal action from the Food and Drug Administration and other regulatory agencies.
- Lost revenue
5 Tips to Improve Exception Management with End-to-End Visibility
In general, customers want their stuff when they want it, and they don’t really want to hear excuses why it will or might be late. That said, most will appreciate a heads-up when things go awry. They realize that stuff happens that is beyond anyone’s control. While it’s impossible to know exactly when and where disruptions will strike, it is possible to flag potential exceptions early. Here are five ways end-to-end visibility can help improve exception management:
- Real-time tracking functionality – Best-in-class trackers provide real-time insights, such as location and condition (temperature, humidity, light exposure, vibration, shock events, tamper detection, and more).
- Configurable alerts – An end-to-end visibility solution should include robust software that focuses on showing the real-time location and condition of shipments, providing alerts if there are issues with any shipment (temperature, delays, etc.)
- Single source of truth – To maximize exception management capabilities, all systems and software in an end-to-end visibility solution should be collaborative and integrated with all the parties involved: shippers, receivers, carriers, and logistics service providers.
- Route optimization – Combine data from multiple shipments and analyze patterns of damage or delays, determine root causes of problems, and optimize future routes.
- Send backup shipments – Early detection via end-to-end visibility provides the opportunity to send a replacement shipment, just in case the first one is indeed compromised.
Take Exception Management to the Next Level with End-to-End Visibility
Implementing in-transit end-to-end visibility will improve overall proactiveness in supply chain exception management. Tive’s proprietary multi-sensor trackers use global cellular connectivity and on-onboard sensors to provide real-time monitoring of shipments to keep all stakeholders informed regarding the location, climate and integrity of their shipments. Tive’s cloud-based software platform gives stakeholders access to that information in real-time and from any device. The ability to configure custom climate and temperature thresholds, along with real-time alerts that will trigger when a shipment exceeds the acceptable ranges puts you a step ahead of the disruption and provides a powerful leg up in exception management. Ready to learn more about the power of end-to-end visibility? Schedule a demo today.