Taking Real-Time Visibility to the Next Level with 24/7 Live Monitoring of Perishable Food & Pharmaceutical Shipments
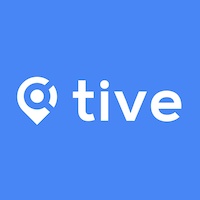
January 13, 2023
March 24, 2025
9 min read
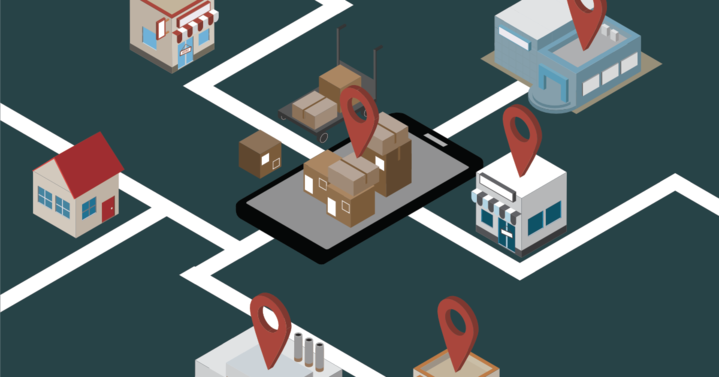
As a shipper tasked with moving temperature-sensitive goods in the high-stakes world of pharmaceuticals and perishable foods, what is peace of mind worth to you?
You undoubtedly understand the basics of cold chain management and the solutions available to gain end-to-end logistics visibility. Simple-to-use temperature loggers may suffice for some shipments; others require the real-time visibility afforded by multi-sensor trackers and dry ice/cryogenic probes to track and monitor a shipment’s location and condition.
Yet there are times when sleep doesn’t come easy—which is understandable when a truckload of beef is valued at $900,000, or a ground-breaking gene therapy carries a price tag of $3.2 million per dose. It would be easy if you could focus on a single, high-value load, but that is hardly ever the case. Consider how many shipments you need to track and monitor daily: 50? 100? More? You can’t watch over every shipment 24/7… nor achieve some semblance of work-life balance that allows for rest along the way.
However, a partner who offers 24/7 live monitoring to augment its robust real-time visibility solutions can help safeguard your pharmaceutical and perishable food shipments—throughout their supply chain journey. This article highlights how the right partner can provide the hardware trackers, software platform, and managed services team needed to give you all the benefits of around-the-clock real-time visibility—without hiring, training, and managing an internal team.
What is 24/7 Live Monitoring?
Round-the-clock monitoring—by a team of logistics experts—is a premium managed service designed to protect shipments and enhance communication with carriers to prevent delays and damage. This team is available 24/7 to assist shippers in the following ways:
Real-time location tracking
This involves monitoring departure, arrival, geofences, proof of delivery, and estimated time of arrival. The team directly contacts the Logistics Service Provider (LSP), carrier, or truck driver to resolve any issues.
Temperature & humidity tracking
The team closely monitors the acceptable ranges for each product. Here, too, they directly contact the LSP, carrier, or driver if an excursion occurs.
Light alerts
A trailer or container getting opened at any point during the journey could be an unauthorized security breach. In such cases, the team contacts all relevant stakeholders.
Monitoring for delayed flights or misrouted shipments
Rest assured, this team will immediately notify you of misrouted or delayed air shipments—and will get shipments on the next available plane if something goes wrong.
Reporting & analytics
Customized dashboards display aggregated shipment information and alert details. You will gain insights to optimize performance, such as on-time carrier delivery.
Challenges of Shipping Perishable Foods & Pharmaceuticals
Perishable foods and pharmaceuticals present several unique and formidable shipping challenges.
- Temperature needs to be regulated during transport
- Conditions must also be monitored to assure quality and safety
- Products must be packaged to prevent spoilage and reduce the risk of contamination from external sources
- All shipments must be tracked and traced to provide assurance they reached their destination—on time and in good condition
- Shipping costs must be carefully managed so that the price of the product remains competitive
Benefits of 24/7 Live Monitoring
Whether you’re shipping pharmaceuticals or perishable foods, a managed services team providing 24/7 live monitoring can help you in several ways.
- Takes the burden off your team. Your staff can focus on serving customers and other tasks to grow the business.
- Helps save shipments. Real-time monitoring and alerts translate into immediate action to preserve the shipment’s quality.
- Improves OTD & OTIF rates. Consistently delivering on time and in full will help you control inventory and logistics costs—and improve customer satisfaction.
- Streamlines carrier collaboration. A managed services team immediately contacts the carrier or driver when a problem arises.
- Reduces customer service costs. A live monitoring team eliminates the need to hire and train additional internal staff, or pay them overtime for round-the-clock coverage.
Now let’s delve deeper into the specifics of shipping perishable foods and pharmaceuticals, the challenges of each, and how 24/7 live monitoring can help shippers overcome them.
Perishable Food Shipping: Feeding an Appetite for Fresh
Perishable foods that require temperature and humidity control during shipping include fruits, vegetables, frozen goods, and dairy products. For example, fruits and vegetables must be stored in refrigerated containers at a temperature between 34 and 40 degrees Fahrenheit. Frozen goods must be kept between 0-10℉. Dairy products must be stored in a temperature-controlled environment to prevent spoilage, typically between 33-41℉. All of these items must be monitored and tracked with technology to ensure the integrity and safety of the product.
Food perishables that must be monitored for humidity include bakery items, fruits, and vegetables. To prevent spoilage, bakery items—such as bread and cakes—require a relative humidity of 50-70%. Fruits and vegetables must be monitored for relative humidity levels between 75-90%, as lower levels can cause the products to dry out and higher levels can cause mold growth.
Current Challenges
- Lack of visibility: Without shipment visibility, shippers and customers are unable to monitor the progress of a shipment and the condition of the product—potentially leading to spoilage and rejected loads.
- Lack of real-time data: Without real-time data, it is impossible to respond quickly to unexpected changes, such as temperature fluctuations or delays, nor can shippers satisfy the Food Safety Modernization Act requirement of 12 months of stored temperature data.
- Difficulty tracking shipments: The inability to track shipments makes it difficult to assure customers of timely delivery, which could lead to empty store shelves and dissatisfied consumers.
Benefits of a 24/7 Live Monitoring Team
- Reduction in product spoilage: 24/7 live monitoring services provide real-time updates on the shipment environment, enabling shippers to take proactive measures to prevent spoilage. Additionally, these services can alert shippers of potential issues before they become a problem, enabling them to take quick corrective action to assure customers of the product’s quality—and ensure that it is safe to consume.
- Complete shipment visibility: Shippers and customers will know a shipment’s location and condition at all times, with the reassurance that a team is ready to take action when needed to prevent product loss.
- Improved data accuracy: Additionally, these services can identify any changes in the environment that would otherwise be undetectable—empowering shippers to make informed decisions based on more accurate and reliable data.
- Increased customer satisfaction: A live monitoring team increases customer satisfaction by providing real-time updates on the shipment environment, enabling customers to monitor the progress of their shipments and the condition of their products. OTIF shipments translate into repeat business—and fewer claims for the shipper to manage.
Pharmaceutical Shipments: How Cold Do You Need to Go?
Shipping pharmaceuticals presents unique challenges, as the temperature and humidity must be carefully regulated to ensure quality and safety. Vaccines, medicines, and cell and gene therapies must be stored at different temperatures and humidity levels. Vaccines typically require temperatures between -4 and 8 degrees Celsius, while medicines and cell and gene therapies must be kept between 2-8℃. Additionally, most pharmaceuticals require between 30% and 60% humidity.
Several pharmaceuticals require ultra-low temperatures using dry ice or cryogenic freezing for safe shipment. For example, insulin must be transported in an environment maintained between -20℃ and -40℃, and anti-cancer drugs require a range of -20℃ to -80℃. In such cases, temperature probes work well with real-time tracking to ensure that the temperature remains within the required range—throughout the shipment.
The most common mode of transportation for pharmaceutical shipments is air transport. Air transport allows for faster transit times and is typically more secure than ground transport, making it the preferred option for high-value and temperature-sensitive shipments.
Current Challenges
- Lack of shipment visibility: Approximately 6-10% of medical shipments by major carriers aren’t delivered on time, and 10-20% of shipments experience problems—many of which can be attributed to a lack of visibility.
- Difficulty tracking shipments: Medical shipments are time-critical and customer-specific. Deliveries that are late—or delivered to the wrong location—could delay life-saving procedures.
- Unexpected delays: Canceled flights and delays happen without notice, jeopardizing shipment quality.
Benefits of a 24/7 Live Monitoring Team
- Improved product safety: An extra set of eyes helps shippers provide assurance that their pharmaceutical products are stored and transported safely and securely.
- Complete shipment visibility: Knowing where shipments are at all times—and communicating that information with doctors, clinics, and hospital staff—is essential to achieving positive treatment outcomes.
- Improved data accuracy: Team members can share real-time location data that stakeholders can use to make informed decisions.
- Reduced compliance risks: Live monitoring support provides added assurance that shipments align with the laws and regulations of the U.S. Food and Drug Administration, the European Medicines Agency, and other regulatory organizations.
Tive’s 24/7 Live Monitoring Managed Services in Action
Tive 24/7 Live Monitoring provides all the benefits of real-time, end-to-end supply chain visibility—without hiring, training, and managing an internal team.
Alpine Fresh: Keeping Things Fresh & Safe
Tive’s 24/7 Live Monitoring managed services give Alpine Fresh the confidence of knowing that the Tive team is on the job around the clock—watching for issues and ready to mitigate as needed—to assure shipments of fresh fruits and vegetables from Latin America arrive on time and in full. “With Tive, there is no guessing game as to whether there is an issue. This saves time and eliminates stress. Everyone can see what’s going on with shipments—and we know the Tive 24/7 Live Monitoring team is constantly monitoring and checking on our behalf,” said Ellie Ivey, Director of Logistics at Alpine Fresh. Read the case study.
Tive’s 24/7 Live Monitoring: Managed Services You Can Count On
Tive understands the challenges of shipping perishable foods and pharmaceutical products—and the pressure shippers face daily to deliver on time and in full. Our industry-leading trackers—including the Solo 5G, the world’s first non-lithium tracker approved by 130+ air carriers—and cloud-based platform provide unparalleled end-to-end cold chain visibility. Yet that might not be enough for shippers who are managing 100 or more shipments at any given time. If you’re in that situation, Tive’s 24/7 Live Monitoring services might just be what you need.
Combining our robust end-to-end visibility solution with live monitoring of location, temperature, humidity, light, and shock will provide you with peace of mind that our team of logistics experts is ready to act on your behalf the moment an excursion happens—no matter the time of day. We monitor your shipments, so you can focus on customer service and growing your business.
Live monitoring is a premium service, but the value of real-time assurance that your products are delivered on time and in full is well worth it. Contact Tive today and put our team of experts to work for you.