10 Best Practices in Cold Chain Management
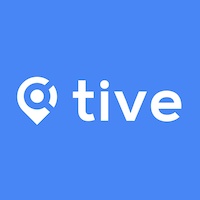
November 12, 2022
March 24, 2025
x min read
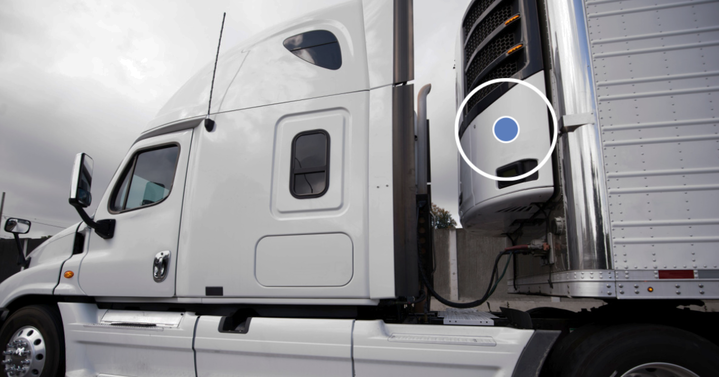
10 Best Practices in Cold Chain Management
Overcoming challenges when handling temperature-sensitive products requires dedication, teamwork, the right partnerships, technology, and communication. Following are 10 best practices to consider including in your cold chain management program.
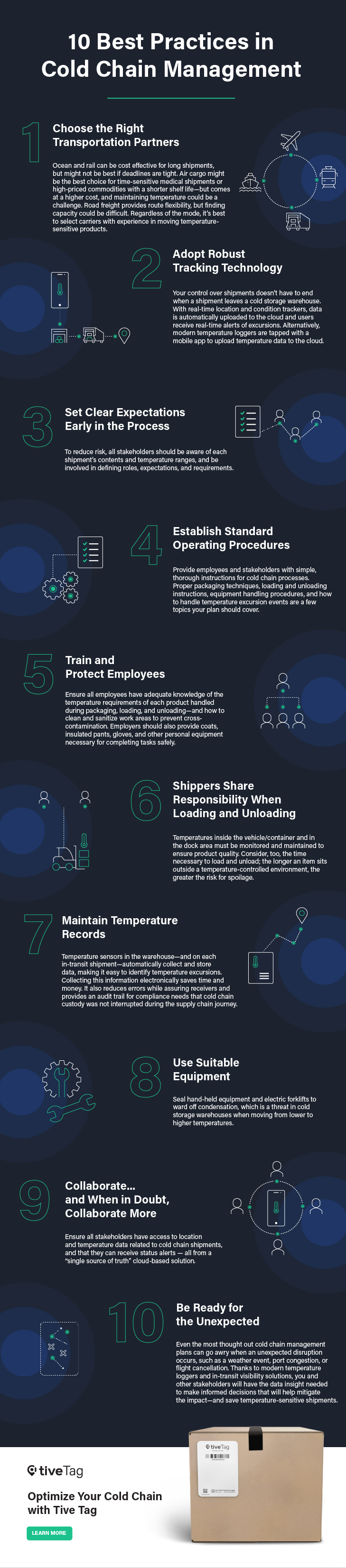
- Choose the right transportation partners: Ocean and rail can be cost effective for long shipments, but might not be best if deadlines are tight. Air cargo might be the best choice for time-sensitive medical shipments or high-priced commodities with a shorter shelf life—but comes at a higher cost, and maintaining temperature could be a challenge. Road freight provides route flexibility, but finding capacity could be difficult. Regardless of the mode, it’s best to select carriers with experience in moving temperature-sensitive products.
- Adopt robust tracking technology: Your control over shipments doesn’t have to end when a shipment leaves a cold storage warehouse. With real-time location and condition trackers, data is automatically uploaded to the cloud and users receive real-time alerts of excursions. Alternatively, modern temperature loggers are tapped with a mobile app to upload temperature data to the cloud.
- Set clear expectations early in the process: To reduce risk, all stakeholders should be aware of each shipment’s contents and temperature ranges, and be involved in defining roles, expectations, and requirements.
- Establish standard operating procedures: Provide employees and stakeholders with simple, thorough instructions for cold chain processes. Proper packaging techniques, loading and unloading instructions, equipment handling procedures, and how to handle temperature excursion events are a few topics your plan should cover.
- Train and protect employees: Ensure all employees have adequate knowledge of the temperature requirements of each product handled during packaging, loading, and unloading—and how to clean and sanitize work areas to prevent cross contamination. Employers should also provide coats, insulated pants, gloves, and other personal equipment necessary for completing tasks safely.
- Shippers and carriers share responsibility when loading and unloading: Temperatures inside the vehicle/container and in the dock area must be monitored and maintained to ensure product quality. Consider, too, the time necessary to load and unload; the longer an item sits outside a temperature-controlled environment, the greater the risk for spoilage.
- Maintain temperature records: Temperature sensors in the warehouse—and on each in-transit shipment—automatically collect and store data, making it easy to identify temperature excursions. Collecting this information electronically saves time and money. It also reduces errors while assuring receivers and provides an audit trail for compliance needs that cold chain custody was not interrupted during the supply chain journey.
- Use suitable equipment: Seal hand-held equipment and electric forklifts to ward off condensation, which is a threat in cold storage warehouses when moving from lower to higher temperatures.
- Collaborate… and when in doubt, collaborate more: Ensure all stakeholders have access to location and temperature data related to cold chain shipments and that they can receive status alerts — all from a “single source of truth” cloud-based solution.
- Be ready for the unexpected: Even the most well-thought-out cold chain management plans can go awry when an unexpected disruption occurs, such as a weather event, port congestion, or flight cancellation. Thanks to modern temperature loggers and in-transit real-time visibility solutions, you and other stakeholders will have the data insight needed to make informed decisions that will help mitigate the impact—and save temperature-sensitive shipments.
The Right Technology Partner Can Help You Handle the Heat of Cold Chain Management
Cold chain management doesn’t just happen. It takes a dedicated team and collaborative supply chain partnerships who believe every shipment matters. It’s impossible to approach it any other way when you’re moving what arguably could be considered the most essential products the world relies on today — temperature-sensitive perishable foods, medicines, and medical products. The world’s demand for those items increases by the day.
We would love to have a deeper discussion with you about how Tive’s industry-leading solutions can help provide the end-to-end cold chain visibility needed for on-time, in-full shipments.
To learn more about our real-time location and condition trackers, let’s start with a demo today.
To learn more about our new affordable, easy-to-use Tive Tag temperature data loggers, click here.