From First Mile to Last: Achieving End-to-End Supply Chain Visibility
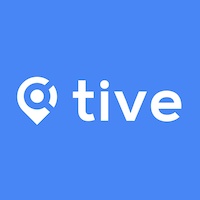
April 8, 2025
July 8, 2025
x min read
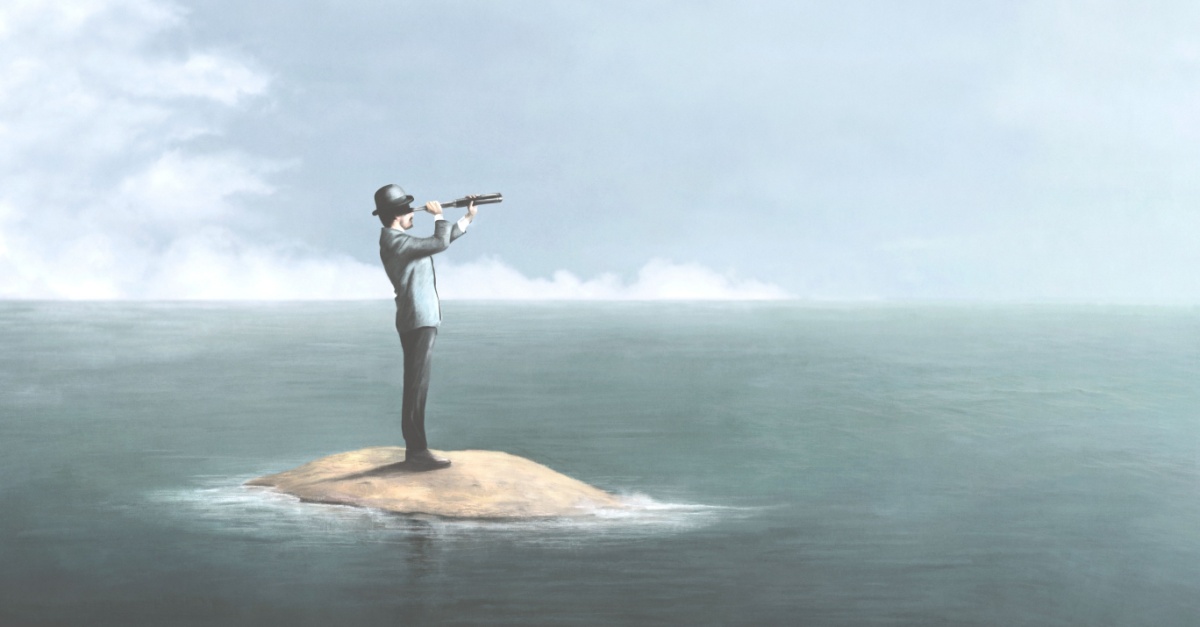
If your shipments had social media accounts, their relationship status would permanently read, “It’s complicated.” And their location? A shrug emoji.
For those of you who’ve devoted your professional lives to moving stuff around the planet, finding end-to-end supply chain visibility is like parking a truck in Manhattan: the mythical quest pursued while downing coffee and stress-eating vending machine snacks at 11 p.m. because someone’s critical component is vacationing at customs.
The dreaded WHERE’S MY STUFF?!! email strikes fear into the heart of every supply chain manager on earth. While the industry excels at tracking departures and arrivals, the middle mile remains logistics purgatory—a black hole where tracking updates vanish, and ETAs become creative fiction.
Tracking technology has evolved from vague “in transit” notifications to systems so precise they detect when drivers hit potholes. And that’s exactly what we focus on in this article: why extending this surveillance across the entire journey matters and how better communication ties it all together.
From First to Last & Everything In Between: The Missing Middle of Supply Chain Tracking
First- and last-mile visibility garners the most attention—and it makes sense why: these are the stages where goods are either being picked up from the supplier or delivered to the end customer. But if you truly want to optimize your supply chain, it won’t happen if you ignore the mid-mile. Unlocking true end-to-end visibility—from door to door—requires a full-fledged approach that bridges all segments of your supply chain.
Paper Trails to Digital Breadcrumbs: First-Mile Tracking Finally Grows Up
Remember when tracking a shipment from its source was like trying to follow a ghost? Legacy systems and manual documentation left us squinting at smudged paperwork—wondering if those goods existed in the first place.
Fast-forward to today: IoT sensors, mobile apps, and integrated management systems have transformed that initial handoff. Now your products leave digital breadcrumbs when they say goodbye to the factory floor. Magic? Nope, it’s just technology finally catching up to common sense.
Real-time shipment visibility, live updates, and cloud platforms mean you’ll know about problems before they snowball. Think of it as catching that first domino before it knocks down your entire supply chain—and saves you from those dreaded “Where’s my stuff?” calls.
Last-Mile Drama: Where Packages Meet Their Destiny (or Your Neighbor’s Bushes)
Customers don’t care about your sophisticated logistics network. They care about the box reaching their doorstep when promised. Period.
The numbers tell the story: According to Tive’s State of Visibility 2025 report, IoT shipment tracking jumped from 55% to 60% in just 12 months. Even better? IoT-based cargo tracking skyrocketed by 200% as companies tossed their clipboards into the recycling bin where they belonged.
The questions keeping logistics pros up at night are surprisingly basic. Which carriers deliver on time? (39% track this obsessively.) Where do packages mysteriously vanish into the Bermuda Triangle? (29% monitor dwell time.) Which routes work without requiring a miracle? (28% benchmark every path.)
Advanced route optimization and AI insights have turned the final delivery sprint from “fingers crossed” to “scientifically optimized.” Those last few miles can make you a hero or villain in your customer’s story—so choose wisely.
The Forgotten Middle: Where Shipments Go to Play Hide-and-Seek
Finally, the middle mile is like that mysterious middle section of a road trip—nobody takes pictures, but it’s where most of the journey happens. While companies brag about their first-mile efficiency and last-mile innovations, Tive’s State of Visibility report also exposes an uncomfortable truth: the middle remains a black hole where shipments play hide-and-seek.
The stats don’t lie: 37% of companies still struggle to track shipments once they’re in transit—essentially throwing their products into the wind and hoping for the best. Even worse? 60% of businesses only discover damage after delivery—or never learn about it at all. That’s like finding out your teenager crashed the car from your neighbor instead of your kid.
The middle mile’s patchwork of carriers, handoffs, and variable conditions creates a perfect storm for things to go sideways. But flip that challenge around, and you’ll find the most significant opportunity for competitive advantage. Solving the mid-mile puzzle multiplies efficiency throughout your entire operation—like finding the missing piece that suddenly makes the whole picture clear.
Companies that apply the same real-time tracking rigor to the middle as they do to the ends achieve that logistics holy grail: true end-to-end supply chain visibility. Your supply chain isn’t a series of disconnected segments after all—it’s one continuous experience.
Best Practices for Proactive Communication & Real-Time Collaboration
Effective communication is at the heart of operational excellence. When everyone—from truck drivers to warehouse managers to impatient customers—knows what’s happening with a shipment, magic happens… or at least there are fewer angry phone calls. And who doesn’t want that?
- Establish clear communication rules: Sometimes, when you played telephone as a kid, the message that started as, “the cat sat on the mat,” somehow ended as, “attack zombies with bats.” Without clear communication rules, your supply chain works the same way. Set up who tells what to whom and when—and watch confusion transform into clarity.
- Get a single tech platform: Nothing screams “disaster” like five different systems showing five locations for the same shipment. A unified platform gives everyone—from Bob in shipping to Lisa, who’s called four times today—the same view of reality. No more awkward “Um, let me check another system” moments during customer calls.
- Make teams talk to each other: Marketing promised overnight delivery. Operations scheduled it for next week. And customer service just poured another coffee and braced for impact. Sound familiar? Regular cross-department huddles stop the chaos before it starts and create supply chain superteams that solve problems—not create them.
- Use data to predict problems: Your AI spotted a pattern: Carrier X + Rainstorm + Tuesday = Late Delivery. Sharing this intel with partners and customers transforms you from the person making excuses to the wizard who knew it might happen—and had plan B ready. People forgive delays they see coming… it’s the surprises they hate.
- Make everyone accountable: Nothing kills progress like the phrase “that’s not my department.” Clear ownership at every shipping stage means problems get fixed—not passed around like a hot potato. Public metrics on performance create healthy competition, because nobody wants to be the team with the sad-looking numbers on the big dashboard everyone sees every day.
Goodbye Shipping Panic. Hello Control.
Supply chains shouldn’t be a guessing game. Nobody wants to explain why that critical shipment is apparently touring Europe instead of arriving at the factory or, worse, becoming another cargo theft statistic. But when you connect every link in your supply chain with concrete data, you’ll stop being the person drafting apologetic emails and start being the one who knows what’s happening and where.
Tive gives your shipments the ability to raise their hand when something’s wrong. Our trackers offer real-time location and condition monitoring, whether your sensitive products are at risk or when your fragile equipment is being handled like a football. Our Tive Tag logs temperature data and ensures your goods remain pristine throughout transit. Then our cloud platform turns this data into usable information, and our live monitoring team jumps in before minor issues become full-blown disasters.
Shipments move through a messy supply chain. But with Tive, you’ll finally know what’s happening when things inevitably get weird—from the first to the middle to the final mile. Get started with Tive today and see for yourself.