Infographic: 10 Critical Challenges in Fresh Grocery & Supermarket Supply Chains
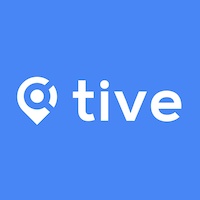
December 15, 2021
March 24, 2025
x min read
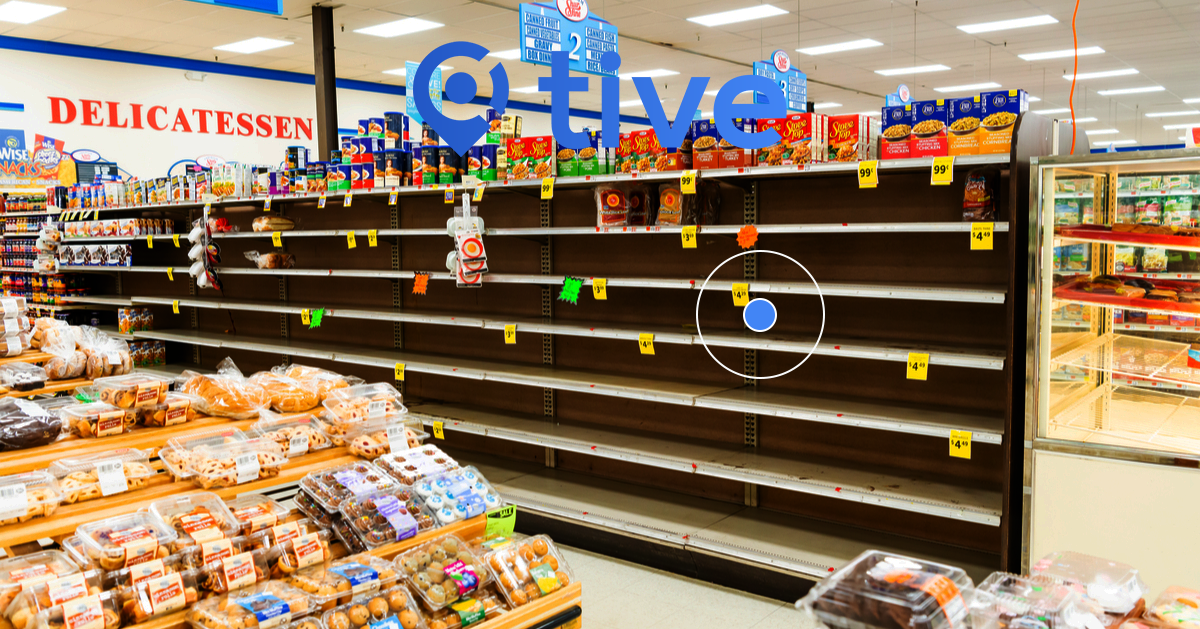
It is no secret that the inability to track a food-related shipment’s location, temperature, humidity, and other factors in real-time while in-transit results in significant losses annually. U.S. grocery retailers estimate that $18 billion in food arrives at their stores spoiled,1 and the U.S. Department of Agriculture states that about 30 percent of food in American grocery stores is thrown away.
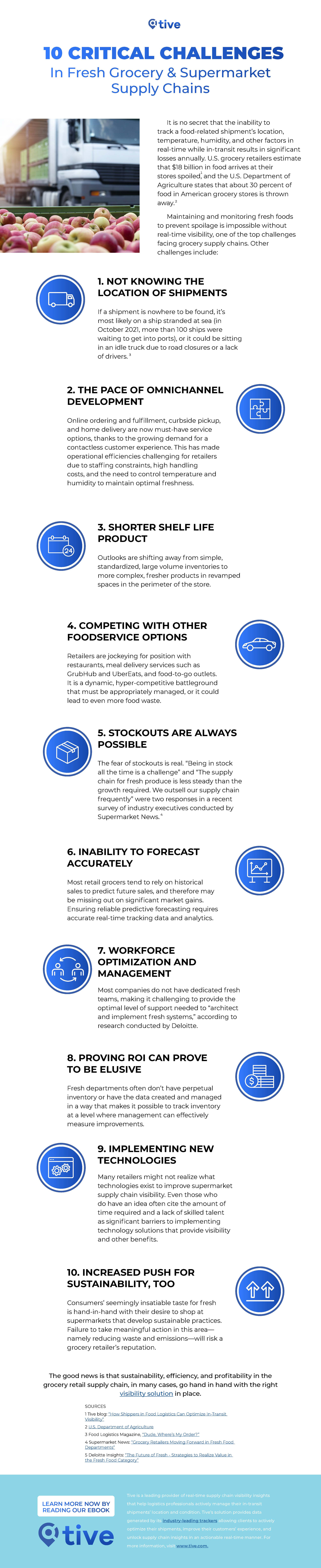
Maintaining and monitoring fresh foods to prevent spoilage is impossible without real-time visibility, one of the top challenges facing grocery supply chains. Other challenges include:
- Not knowing the location of shipments: If a shipment is nowhere to be found, it’s most likely on a ship stranded at sea (in October 2021, more than 100 ships were waiting to get into ports), or it could be sitting in an idle truck due to road closures or a lack of drivers.3
- The pace of omnichannel development: Online ordering and fulfillment, curbside pickup, and home delivery are now must-have service options, thanks to the growing demand for a contactless customer experience. This has made operational efficiencies challenging for retailers due to staffing constraints, high handling costs, and the need to control temperature and humidity to maintain optimal freshness.
- Shorter shelf life product: Outlooks are shifting away from simple, standardized, large volume inventories to more complex, fresher products in revamped spaces in the perimeter of the store.
- Competing with other foodservice options: Retailers are jockeying for position with restaurants, meal delivery services such as GrubHub and UberEats, and food-to-go outlets. It is a dynamic, hyper-competitive battleground that must be appropriately managed, or it could lead to even more food waste.
- Stockouts are always possible: The fear of stockouts is real. “Being in stock all the time is a challenge” and “The supply chain for fresh produce is less steady than the growth required. We outsell our supply chain frequently” were two responses in a recent survey of industry executives conducted by Supermarket News.
- Inability to forecast accurately: Most retail grocers tend to rely on historical sales to predict future sales, and therefore may be missing out on significant market gains. Ensuring reliable predictive forecasting requires accurate real-time tracking data and analytics.
- Workforce optimization and management: Most companies do not have dedicated fresh teams, making it challenging to provide the optimal level of support needed to “architect and implement fresh systems,” according to research conducted by Deloitte.
- Proving ROI can prove to be elusive: Fresh departments often don’t have perpetual inventory or have the data created and managed in a way that makes it possible to track inventory at a level where management can effectively measure improvements.
- Implementing new technologies: Many retailers might not realize what technologies exist to improve supermarket supply chain visibility. Even those who do have an idea often cite the amount of time required and a lack of skilled talent as significant barriers to implementing technology solutions that provide visibility and other benefits.
- Increased push for sustainability, too: Consumers’ seemingly insatiable taste for fresh is hand-in-hand with their desire to shop at supermarkets that develop sustainable practices. Failure to take meaningful action in this area—namely reducing waste and emissions—will risk a grocery retailer’s reputation.
The good news is that sustainability, efficiency, and profitability in the grocery retail supply chain, in many cases, go hand in hand with the right visibility solution in place.
Learn more now by reading our ebook.