5 Visibility Gaps in Your Supply Chain (And How to Fill Them)
September 19, 2017
March 24, 2025
x min read
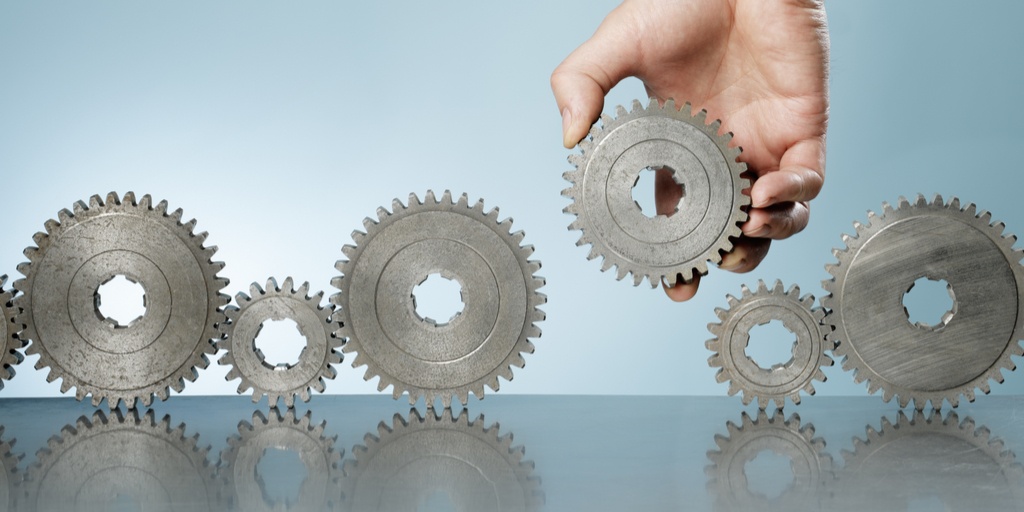
Here at Tive, we talk about supply chain visibility all the time. It’s the key to optimizing a supply chain, to getting the awareness you need about the location and condition of your shipments.
But what does it mean for you? Here are five real-world examples of common visibility gaps we’ve seen in our customers’ supply chains.
Stuck at the Port
Modern international ports process thousands of containers every day. They are impressively complex operations, and it’s no surprise that containers occasionally get lost in the shuffle. Unfortunately, if it’s your container that’s stuck at a port, you probably have no idea where it is, why it’s been held up, and if there’s anything you can do about it. This may result in delays downstream in the supply chain, delays for customers receiving the end product, extra costs, and a whole lot of headache for the supply chain manager. Shipments stuck in port - sometimes for weeks on end - present a serious dark spot in the supply chain. A real-time tracking solution can shed light on these visibility gaps, giving you insight into the precise location of your goods so you can react to delays and solve problems right away (be it through a phone call to the port, rerouting another shipment, or a proactive customer communication).
Or Just Stuck in Traffic
Without real-time visibility, a shipment stuck at port and a shipment stuck in traffic might look the same. After all, as far as you and your customer are concerned, a late shipment is a late shipment. If a shipment is delayed and you don’t know why, you may be forced to implement expensive backup measures, such as rerouting another shipment, as soon as possible. But if it turns out the delay is only a few hours due to traffic, and not a few weeks or months due to a hold up at the port or in customs, then your backup measures may be completely misplaced. If you know the location and condition of your shipment, then you gain insight into the cause and expected duration of a delay, enabling you to make an informed (and ultimately less costly) response.
Waiting on the Tarmac
In general, you know what flight your goods will be on, and when the plane is expected to depart and arrive. But that doesn’t mean you know everything that happens while the shipment is getting from point A to point B. What if your shipment is held up in processing? It may be delayed, but worse yet, if it is temperature-sensitive, an unplanned waiting period, potentially on a hot outdoor tarmac, could be disastrous. Your goods could show up irreparably damaged, with no insight as to why or when the damage occurred. Real-time awareness of the location and condition of your goods makes it easy to figure out what happened and avoid the problem in the future, and may even enable you to make a call as soon as you see the temperature is off and avoid the damage altogether.
Temperature Excursions en Route
Of course, the tarmac’s not the only place where unexpected temperature fluctuations pose a threat to temperature-sensitive shipments. A reefer’s cooling system may malfunction, or be set incorrectly, or goods may be removed from their containers for inspections or other unplanned processing. With traditional temperature loggers, you won’t find out about the problem until after delivery - and even once the shipment is delivered, the logger data will need to be uploaded, sent to you, and analysed. By then, it is too late. The product is damaged, and it will take time and money to replace it. With real-time supply chain visibility, you can see a temperature excursion as soon as it occurs, and you can act accordingly: call the trucking company to reset the temperature, reroute a backup shipment to avoid delays for the end customer, or whatever other proactive remedies you have at your disposal.
The Last Mile
Although it’s the shortest and quickest leg of your product’s journey, the last mile is often the most important, and the least visible. Even if your supply chain is almost totally flawless, unexpected delay or damage to the product in the final stages of delivery can ruin the end customer’s experience. And that’s a big deal -- a recent study found that almost fifty percent of online shoppers declined to shop again at a retailer if their shipment arrived damaged or delayed. Real-time awareness of the location and condition of your product, all the way from origin to final destination, gives you the insight you need to build effective contingency plans and resolve problem shipments, often without the customer even realizing there was an issue at all.
Filling Your Visibility Gaps
The modern supply chain is complex, global, multi-modal -- and full of visibility gaps. The dark spots in your supply chain cost you time, money, and reputation, as you’re forced to run a business with incomplete awareness as to where your goods are and how they are doing. To succeed in this environment, managers must incorporate modern digital solutions that provide real-time visibility into a supply chain’s hidden corners, enabling potential problems to be discovered and avoided before it’s too late.
For more information on how Tive can help you fill the visibility gaps in your supply chain, request a demo today.