Love Is Blind, But Your Valentine’s Day Supply Chain Shouldn’t Be
February 14, 2018
March 24, 2025
x min read
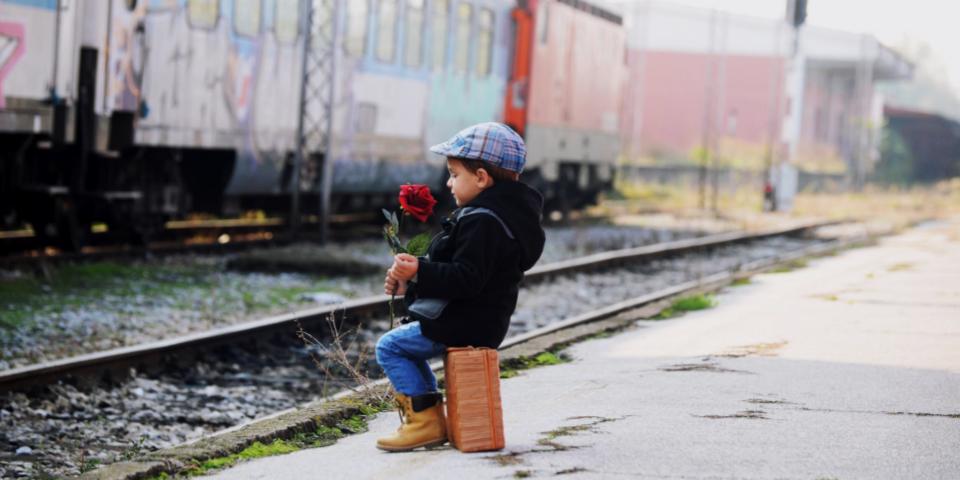
Every year, as couples (and hopeful bachelors and bachelorettes) gear up for Valentine’s Day, more than 95 million flowers are shipped all around the world. That’s three thousand tons of flowers. With millions of hearts relying on successful delivery, making sure those flowers get where they need to go, on time and undamaged, is no small feat.
The need for timely delivery is clear. No one wants roses on February 13th, and heaven forbid your bouquet doesn’t arrive until the 15th. Avoiding damage is equally important in the Valentine’s Day supply chain. Most flowers are shipped from Central America to the U.S., and must stay within precise temperature bounds to avoid wilting. This can be particularly challenging as many shipments must pass through customs inspections and be moved between various modes of transit. For one unfortunate company, a temperature malfunction last February lead to an entire truckload of flowers arriving to their disappointed recipients frosted, brown, and wilted -- not a great recipe for successful courtship.
Mishaps like these emphasize the need for comprehensive supply chain visibility, especially for time-sensitive, quality-sensitive products. With many last-minute orders placed just days or hours before delivery, real-time awareness of the location of each shipment is key to making sure that every bouquet finds its way to the appropriate location in time. And with goods so susceptible to even slight variations in environment, it is vital to maintain non-stop awareness of temperature, humidity, and other key metrics. That way, if a malfunction does occur, the faulty refrigerated container can be fixed, replaced, or at the very least the damaged goods can be replaced before delivery.
So how do you achieve this level of real-time supply chain visibility? A combination of always-connected tracking devices and a cloud-based software platform can provide access to the data you need, when you need it. Trackers can monitor location, climate, and shipment integrity, and send that information directly to your phone or email, enabling immediate awareness of up-to-date shipment status and potential issues. For example, if a shipment is delayed or experiences a temperature excursion, you can receive an alert right away, giving you the heads up you need to solve the problem and mitigate fallout.
Although most of our customers deal with more industrial, less romantic goods, the principles of supply chain visibility are the same. Whether you are shipping high-value pharmaceutical goods or a pallet of roses, knowing where your stuff is and how it’s doing is key to managing a successful supply chain. To learn more about how Tive can take the surprises out of your supply chain, request a demo today.