Beyond Location — Condition of In-transit Shipments Is Critical
January 20, 2021
March 24, 2025
x min read
.jpeg)
The supply chain visibility movement is gaining massive traction, and you likely have a handle on monitoring where your shipments are in transit. But do you know how your shipment is?
Are you confident your perishable goods are staying cold? Were you alerted that your electronic equipment load may have been damaged due to shock? Or humidity? Was the container opened at an unauthorized location?
It's no longer enough to know just where your load is. In today's shipping landscape, actively managing the condition of your load is an important competitive advantage.
Shipment Condition is Critical
As customers' expectations rise, in-transit visibility has evolved beyond location to include the load's condition - a critical element. In our always-on world, customers want to know their products and assets will arrive both on-time and in full. FreightWaves calls it "Beyond Dots on a Map."
Let's say you're transporting fresh strawberries. If the berries get too warm or too wet in transit, the entire load may spoil and be rejected upon arrival. You can read more on temperature control at United Fresh. However, with in-transit visibility that allows you to monitor conditions like temperature, light, shock and humidity, you can catch the exception in real-time, enabling you to communicate with the driver to check the truck's reefer unit. A timely adjustment or repair can save the load, averting a loss of hundreds of thousands of dollars.
Spoiled perishables, delayed shipments, product shortages - these pitfalls cost customers money, time, and energy. And ultimately, they can cost you business. Tive's in-transit visibility solution puts you in the drivers' seat to know immediately when optimal conditions aren't being met. Armed with actionable analytics and insights, you exceed rising customer expectations and improve their experience.
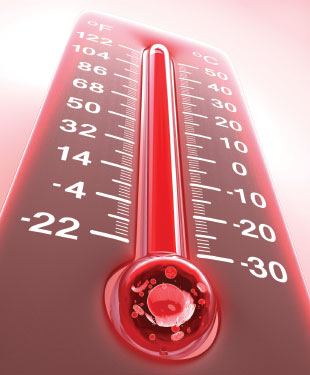
There's No Time Like the Present
Retrieving condition data like temperature, humidity and shock from trackers at the end of a shipment is too late. When sensitive and high-value goods are exposed to conditions outside the prescribed range for transport, entire loads may be damaged, lost or detained. That's why real-time insights and proactive alerts are critical. They inform you when:
- a load is too hot/cold or too wet;
- a potentially harmful shock level is experienced;
- a trailer or box has been opened.
These real-time insights, combined with around-the-clock monitoring and 24/7 support allow logistics professionals to intervene and solve potential problems when, or before, they occur.
Take, for example, a shipment of high-value televisions. If you receive an alert that a box or trailer is opened outside of a scheduled location or time (monitored through light sensors), it may indicate a possible theft. With this in-the-moment insight, you can immediately investigate or work with local authorities to intervene, preventing the potential loss of valuable products.
Going Beyond Location
Visibility into shipment location has become a must-have in recent years. The competitive differentiator now is in-transit visibility and professional support that is an extension of your logistics team.