How Electronics Shippers Are Gaining Visibility with In-Transit Trackers
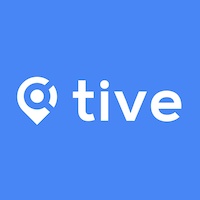
March 7, 2023
March 24, 2025
x min read
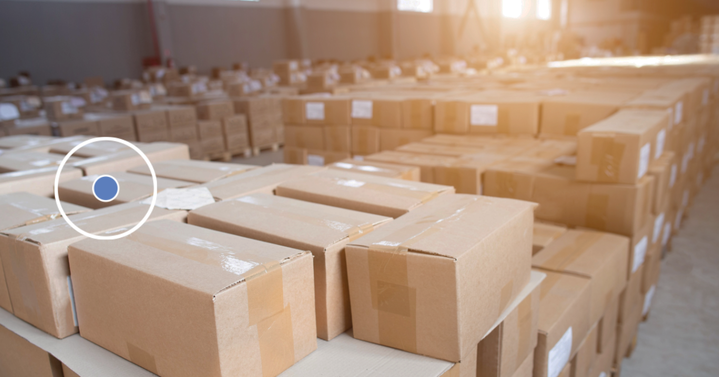
Electronics shipping is an endeavor filled with obstacles for companies delivering functional devices to their customers. Global uncertainty in recent years has exacerbated the challenges, as a recent study found that over 50% of companies face logistics and transportation supply chain problems, while nearly 40% lack the necessary manufacturing capacity to meet demand. Consider the challenges a company faces when sending electronic goods to customers in another country: The process involves coordinating with various partners and ensuring the products are delivered on time and in good condition—and with no defects. Any mishap may result in significant setbacks and cause damage to the company’s reputation.
Electronic shippers are under more pressure than ever, and shippers must develop strategies to deliver on time and in full—every time. Shippers must remain agile and alert to various obstacles that may arise. This article explains the difficulties facing the electronics supply chain, how investing in visibility builds the resilience and flexibility to handle these challenges, and how Tive’s digital trackers and innovative technology provide hyper-accurate, real-time visibility—along the length of the supply chain—to ensure electronics arrive on schedule, fully functional, and ready to enjoy.
Critical Challenges in Electronics Shipping
Marking “fragile” on shipments doesn’t ensure they will be handled delicately and carefully. Shippers must be proactive and take the initiative in planning safe shipping by using proper packaging and shipping materials and by insuring shipments, as required. Companies’ challenges include a need for more transparency, ever-rising costs, global shortages, and changing regulations. China exports over $500 billion in goods to the United States yearly, and any slowdown or delays in those supply chains—especially when dealing with semiconductors—cause setbacks. The following are three main sets of challenges that shippers face.
The difficulty of shipping fragile goods
Electronic devices are extremely heat and moisture sensitive, making them vulnerable to damage during shipping. Even a tiny amount of water exposure or extreme temperatures may cause the devices to malfunction. Electronics are also prone to shock damage; devices that fall and hit the ground can result in cracked screens or damaged internal components. Electronics with sensitive components are also susceptible to problems that aren’t noticeable until they are in the hands of the consumer. Transporting electronics with care is crucial to mitigate these risks, including specialized packaging and handling methods. Shippers must take appropriate measures to ensure that products are delivered in perfect condition—to achieve total customer satisfaction while minimizing product damage and repair costs.
The difficulty of obtaining vital components
Obtaining components can be challenging—and can significantly disrupt the entire supply chain. Semiconductors, for instance, are a critical part of electronics and can be difficult to source. The semiconductor supply chain is often limited due to a complex and lengthy manufacturing process, and it is considered one of the top supply chain risks of 2023. The United States manufactures only 12% of the worldwide supply, putting it at the mercy of international shipping—where control regulations, increased demand, labor shortages, and global strife cause delays that ripple through the supply chain. To avoid such issues, companies need solid contingency plans, including working with multiple partners who provide the necessary goods when required to meet customer expectations. Monitoring inventory levels closely is crucial to avoid shortages and delays. These measures help ensure that the supply chain continues to operate smoothly, even when faced with unexpected challenges.
The difficulty of supply chain collaboration
Electronics shipping is increasingly reliant on logistics partners for timely manufacturing and delivery. Unfortunately, many standards do not include the protocols necessary for sharing actionable insights vital to building resilient and collaborative supply chains. This lack of collaboration often leads to delays and increased costs. Electronic devices may involve multiple components from various suppliers—making cooperation between parties essential. Clear and open communication is necessary to establish trust and enhance relationships. When supply chain partners don’t readily share information, everyone suffers. Companies must prioritize collaboration and develop effective communication channels with all partners to overcome these challenges. This includes building a culture of transparency and trust. By working together, companies streamline the supply chain, reduce delays and costs, and deliver high-quality products that meet customer expectations.
How In-Transit Trackers Provide Electronic Shippers With Container-Level Visibility
There are many ways things can go wrong when dealing with shipping electronics around the globe—but solutions exist that can combat these issues. One available solution is in-transit trackers that provide unprecedented visibility into shipping from origin to destination. Companies can easily trace and track shipments using these trackers to ensure quality and meet customer expectations. Real-time trackers enable companies to identify potential problems—and make informed decisions quickly. Meeting the evolving needs of customers leads to consumer loyalty and hundreds of companies the benefits of Tive trackers every day. Following are four ways in-transit trackers can help alleviate supply chain woes:
Fragile Goods Arrive Safely
Using real-time trackers like Tive’s Solo 5G Trackers, up-to-minute freight status is no longer a mystery. Tive trackers provide real-time information about the location and condition of freight, including temperature, humidity, shock, and light—indicating the number of times the load doors have been opened. These trackers transmit data to a cloud-based platform that is available to all parties involved, ensuring that fragile electronics remain under surveillance throughout transit. Stakeholders can use this data to make decisions and act quickly to fix any issues that arise, preventing delays and potential damage to the products. Proper tracking is crucial for companies that want to avoid delays and optimize shipping routes. Any deviation from the original plan can spell doom for fragile goods, especially if the damage isn’t noticed until too late. With Tive trackers, companies can monitor shipments and make informed decisions to ensure the safety of products. In addition, customers benefit from increased transparency and improved peace of mind—knowing that their electronics are tracked and monitored throughout the process.
Cargo is Protected from Theft
Cargo theft is an ever-growing problem. Not only does theft cost companies the loss of the current shipment, but it can also wreck production cycles, and even trigger recalls depending on the type of cargo. Transfer points—and the final miles of a journey—are often the most dangerous. Real-time visibility reduces the chance of shipments being stolen by enabling companies to monitor freight the entire way and detect any possibility of theft. If there are unexpected deviations from the original route or the cargo doors are being opened too often, stakeholders can take immediate action to discover what has gone amiss—and start the recovery process, if necessary. To learn more about how to prevent theft with the help of real-time visibility, sign up for this March 16 webinar: Do You Know Where Your Shipments Are? How Visibility Technology Can Mitigate Cargo Theft and Security Risk.
Vital Components are Tracked With Real-Time Visibility
Tracking vital components with real-time visibility greatly benefits stakeholders along the supply chain. Tive Solo 5G trackers are cutting-edge tools that offer real-time visibility and alerts via a cloud-based platform, making it easier to ensure that electronics arrive on time and in excellent condition. With hyper-accurate container sensor tracking, shippers may pinpoint precisely where a container is within the supply chain—and can monitor its status and condition. This capability enables shippers to adapt to the unpredictable nature of the supply chain process. Real-time visibility also enables improved route optimization, spurs cost savings, improves customer service, and provides insights gleaned by studying real-time shipment data. By maintaining constant visibility throughout the supply chain, organizations can anticipate potential issues before they arise. By leveraging advanced tools like the Tive Solo 5G, companies can minimize delays and deliver high-quality products that meet customers’ demands.
Electronics Supply Chain Collaboration is Optimized through In-Transit Visibility Platforms
By facilitating complete, end-to-end collaboration, n-transit trackers are a game-changer for the electronics supply chain. With advanced software and unparalleled visibility, companies achieve new levels of coordination and transparency, ensuring all partners stay informed about the real-time status and condition of shipments. A cloud platform is crucial in making all this possible because it provides regular updates to all interested stakeholders. This level of transparency allows partners to coordinate their activities and work together to ensure electronics arrive on time and in good condition.
If something goes awry during transport, in-transit trackers will enable an audit trail so that everyone can understand what went wrong—and cooperate to ensure the issue gets resolved for future trips. Suppose electronics cargo is on a ship that encounters a massive storm in the South Pacific. In that instance, stakeholders can follow the events on the platform—in real-time—and quickly work together to find a solution, adjusting plans and rerouting shipments to ensure on-time delivery while being reassured that the load hasn’t suffered any damage on the rocky seas. The ability to anticipate potential problems—and strategize together for a more agile, resilient supply chain—is invaluable. By leveraging these tools, companies mitigate risks, reduce delays, and ultimately deliver better customer results.
Exceed Your Electronic Shipping Needs With Tive’s Real-Time Tracking Capabilities
The tiny components contained inside all electronics help the world function, and civilization as we know it could grind to a halt if problems during shipping go unchecked. As such, the importance of real-time visibility and collaboration in electronics shipping cannot be overstated. Without the real-time insight provided by digital, in-transit trackers and cloud software solutions, delicate components might be damaged—causing delays and increasing costs. Tive’s visibility solutions—including condition monitoring, hyper-accurate location tracking, and real-time collaboration—help supply chains thrive in the ever-changing world of shipping electronics.
Electronics shipments lacking real-time trackers may be doomed from the start, leading to negative customer responses and a hit to the company’s bottom line. Get started with Tive today, and see how in-transit tracking can help your business take action—in real-time—to deal with any sudden difficulties. Partner with Tive today and optimize your electronics supply chain. By doing so, you can be confident that your electronics will arrive on time and in full, no matter the challenges that arise.