Cut Costs, Not Corners: Reducing Transportation Costs with Real-Time Tracking & Monitoring
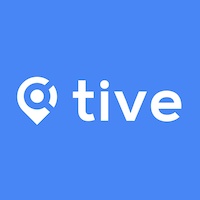
May 21, 2024
March 24, 2025
x min read
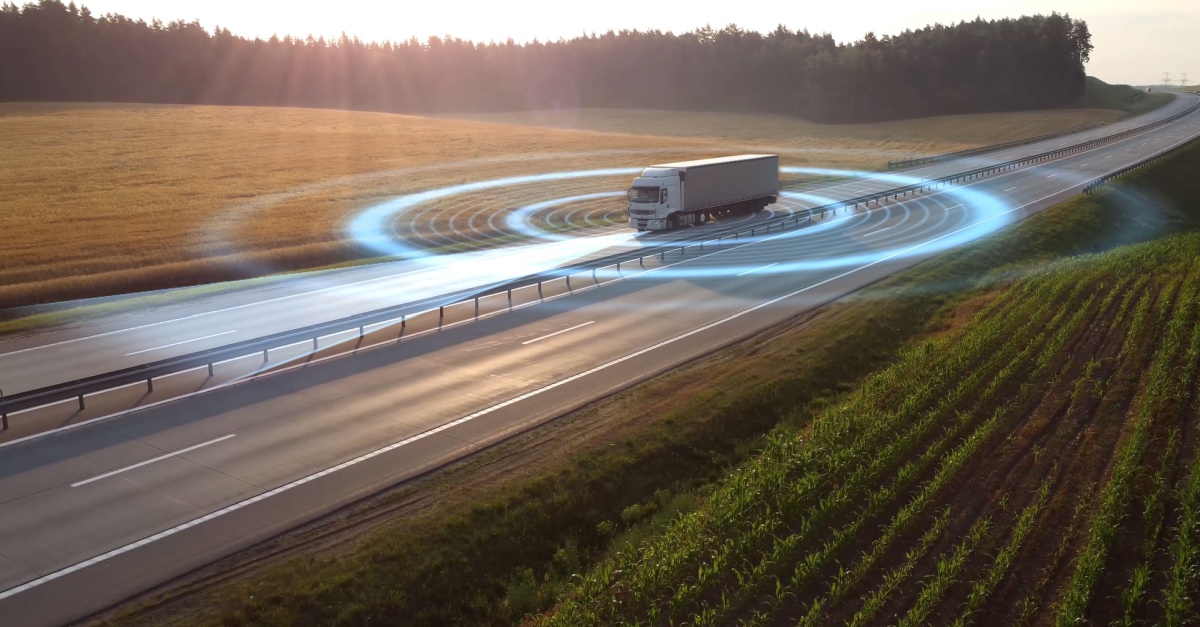
Transportation costs are skyrocketing, and everyone’s feeling the pinch. Labor strikes over harsh penalties, pay, and working conditions have caused delivery delays and shortages—driving up freight costs. Layoffs due to a manufacturing slowdown and disruptions in Middle Eastern shipping routes have also played a role.
The worst part? There’s no end in sight. Logistics costs in Q2 2024 have been surging dramatically. A UPS report showed that 74% of shippers expected outsourcing expenses to rise by 5% to 10%. Freight rates have shot up, with Asian to North European rates spiking 173%, and carriers are tacking on surcharges up to $2,700 per container.
So, what’s the fix? Perhaps real-time tracking and monitoring.
The Hidden Costs of Cutting Corners
Everyone loves saving money, but with transportation, cutting corners can end up costing more in the long run. The initial savings might be tempting, but hidden transportation costs—from damaged products to theft—can snowball, impacting your bottom line in ways you might not have anticipated.
The Price of Product Damage
Overlooking real-time tracking might save you some money upfront—but it can lead to expensive problems down the road. Without real-time visibility, goods are more likely to get damaged during transport or storage. Old-school inventory methods are full of errors and can lead to overstocking or stockouts—both of which can damage your products, add unforeseen costs, and negatively impact customer experience.
Moreover, it’s hard to predict demand accurately when inventory levels are off. This results in poor planning and wasted resources, which can cause further product damage and unnecessary costs. On average, damages cost businesses around $0.60 for every $1,000 of goods transported. While that might not seem like much, it adds up quickly and can lead to significant lost revenue.
Beyond the direct costs, handling and storing replacement goods and managing returns and refunds can hit your wallet. Damaged goods also hurt your brand’s reputation and customer loyalty, leading to lost sales and long-term financial pain.
The Cost of Cargo Theft & Fraud
Cutting corners on security can also lead to serious theft problems that cost your business dearly. It’s rough enough that the average stolen shipment costs $281,757 and leads to a total loss of $154.6 million. But what’s worse is how cargo theft and fraud are rising. CargoNet data reveals 925 incidents reported in the first quarter of 2024 alone—a 46% year-over-year increase—and those are only the reported incidents. Illinois, California, and Texas are seeing the biggest spikes, with increases of 126%, 72%, and 22%, respectively. Though food and beverage shipments are the prime target for cargo theft today, thieves also target high-value items including small appliances, liquor, energy drinks, and copper.
These thefts directly increase transportation costs. To protect their goods, businesses are forced to spend more on security measures and insurance premiums. Otherwise, companies face lost sales and must raise prices to compensate for the losses. Theft also disrupts supply chains, causing delays and extra costs for rerouting shipments or expediting replacements.
Unscrupulous Practices by Brokers & Carriers
Brokers and carriers sometimes use shady tactics—including deceptive rate negotiations and double brokering—to protect their margins, leaving you with unexpected costs and frustrations. Real-time tracking steps up by providing transparency and accountability—so you know exactly where your shipments are and who is handling them.
Deceptive Rate Negotiations & How Real-Time Tracking Can Help
When it comes to costs, dealing with brokers can sometimes feel like a game of hide-and-seek. They might offer you a rate based on package type, weight, service level, distance, and delivery type—but then sneak in hidden fees for fuel, insurance, and other expenses. This lack of transparency can leave you with unexpected bills and frustration.
Real-time tracking can make a big difference by providing accurate data on travel times, distances, and delays. With GPS and IoT devices, you always know where your shipment is. When a parcel is scanned and loaded onto a vehicle, its position is constantly updated. This transparency helps you spot delays and bottlenecks, making scheduling more reliable. Plus, with clear data, you can push back against unfair fees and demand fair rates—ensuring you’re not caught off guard by hidden costs.
The Dangers of Double Brokering & How Real-Time Tracking Can Help
Double brokering is a sneaky practice where a broker wins a bid for a load—and then hands it off to another carrier without telling the shipper or the original broker. Unsurprisingly, this can lead to stolen shipments and significant financial losses: $500 million to $700 million in freight each year. It’s also a rising trend. Complaints about double brokering shot up 400% from late 2022 to early 2023. A recent survey also revealed that double brokering impacted 85% of respondents. 56% of respondents lost up to $50,000, while 18% lost between $50,000 and $150,000.
Real-time tracking helps stop double brokering by providing constant shipment visibility—empowering shippers to verify who their carriers are, and to track their shipments from pickup through delivery. This transparency means you always know who's handling your freight and where it is, reducing the risk of unauthorized brokering. Real-time tracking also helps spot delays and bottlenecks, which makes scheduling more accurate and keeps you updated—all while protecting against financial losses.
Real-Time Tracking & Monitoring: It’s an Investment, Not a Cost
Think of a logistics company that knows exactly where every shipment is—all the time. It's not always cheap to make it happen, but it’s a game-changing investment with benefits that pay off in the long run. You can leverage real-time tracking and monitoring to save money, boost efficiency, and keep customers happy in several tangible ways:
- Implement IoT for real-time tracking and monitoring: IoT devices—such as sensors and RFID tags—provide real-time data for clear visibility and inventory management accuracy. This translates to faster deliveries, less wasted inventory, and higher profits. Capgemini found that 70% of organizations using IoT in their supply chains saw increased efficiency.
- Leverage AI for predictive analytics and route optimization: AI looks at past data to predict future trends, helping you better plan inventory and workforce needs. AI also identifies the best delivery routes, reducing errors by 20-50%—and cutting lost sales and product shortages by up to 65%.
- Integrate automation systems to streamline operations: Automation in logistics handles large data sets, optimizes routing, and smooths out processes—leading to quicker deliveries and fewer mistakes. Automated warehouses using robotics can save a lot on costs.
- Use blockchain for better visibility and security: Blockchain speeds up deliveries, improves product traceability, and enhances partner coordination—leading to lower costs across the board. By 2025, 20% of top global grocers will use blockchain for food safety and traceability.
- Utilize big data and analytics for real-time insights: Big data helps optimize real-time routes and schedules, making smarter decisions and operations more efficient. There’s a reason why roughly 74% of supply chain executives consider big data analytics one of the most crucial supply chain and logistics technologies.
Revolutionize Your Logistics with Real-Time Tracking
Real-time tracking and monitoring are essential technologies for reducing and optimizing transportation costs. With logistics expenses soaring and freight rates through the roof, businesses need these tools now more than ever. But it’s on you to stop cutting corners—and see beyond the initial investment. By adopting real-time tracking, companies can make smarter choices, manage inventory more effectively, and ensure timely deliveries. The benefits will pay off, but the time to embrace these technologies is now.
Tive has you covered. Tive’s Solo 5G trackers provide real-time updates on your cargo’s location and condition, so you always know your shipments are safe and secure. The reusable Tive Tag data logger provides location and temperature visibility—as well as an audit trail of temperature data during transit for perishable goods. Tive's user-friendly cloud platform offers complete visibility and analytics for your supply chain. Plus, the Tive 24/7 Live Monitoring team can constantly watch your shipments—guaranteeing they arrive on time and in full.
Ready to transform your logistics? Book a demo and contact Tive today to get started!